Artificial Intelligence (AI) will change fisheries in many ways. The advent of convolutional neural networks (CNN) has dramatically increased the power of computer vision systems used for stock assessments and bycatch monitoring. Other software programs interpret engine data and vessel performance data to increase efficiency and reduce maintenance.
While onshore processors have begun to use AI and machine learning to increase quality, the last place AI shows up is in the onboard seafood processing systems. Carsoe Industrial Machinery Manufacturing in Aalborg, Denmark, has long been a leader in onboard processing systems. It intends to lead the way in getting AI and machine learning (ML) solutions into its products. “We consider it a decisive factor in remaining the most relevant supplier of process equipment and service in the future,” says Johan Schwerin, group service director at Carsoe. “The first step on this journey is reliable data collection and storage to make data available for an analysis process powered by AI.”
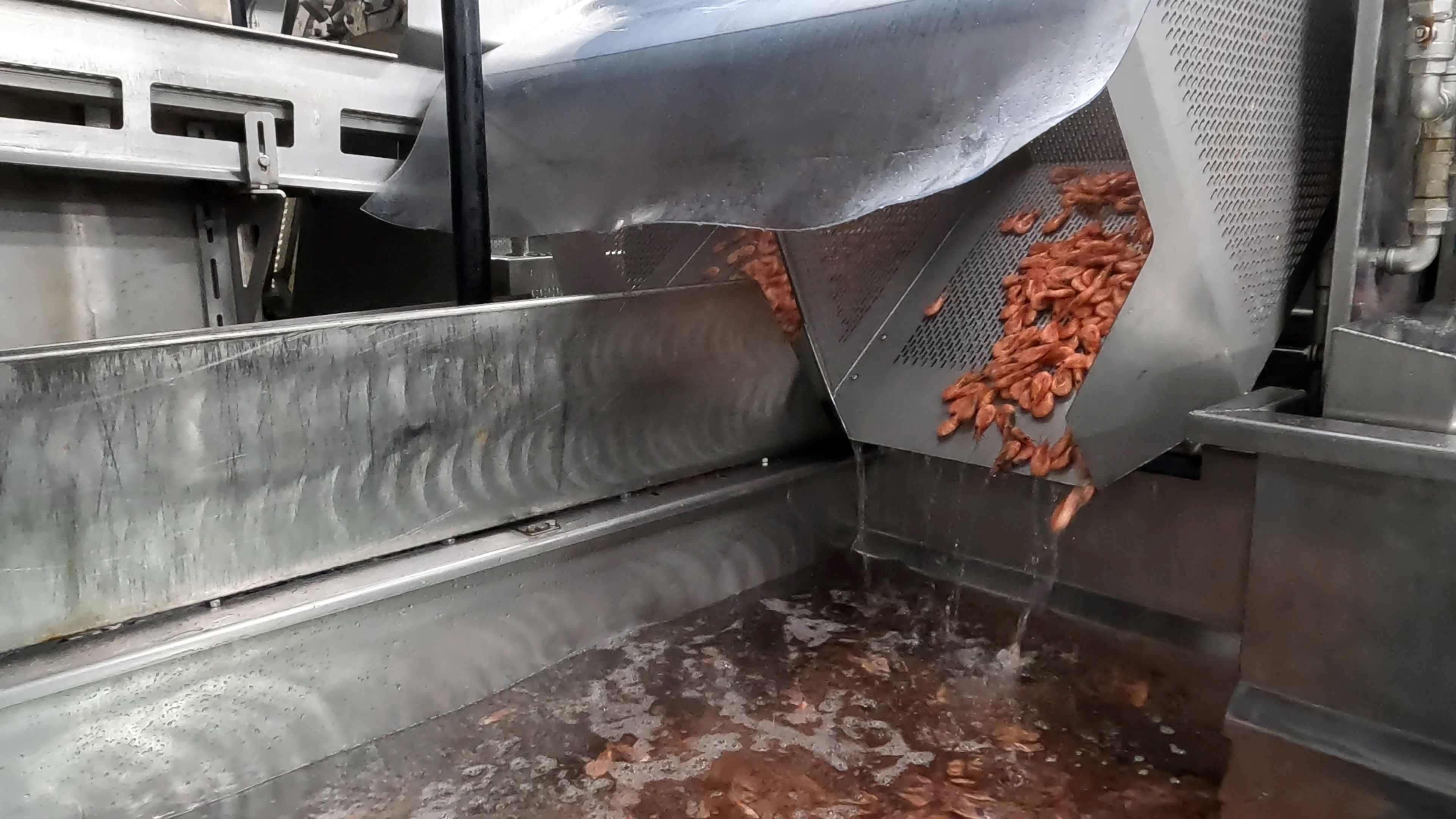
“Carsoe is a turnkey processing systems manufacturer,” says Schwerin. “Our systems handle the fish from the time they come aboard until they are offloaded in port. So, we already have a high level of technology on board, and from that, we can collect a lot of data. By feeding this data to AI and ML, we have an opportunity to support quality improvement.”
Schwerin notes that while the systems Carsoe provides to a fleet of vessels may be identical, quality is not. “Even on the same vessel, with different crews, we see differences in quality. Adjustments to the process are made based on the experience of the people running the machinery, creating a lot of variation. What we want to do is create a recipe to get the highest quality out of this scarce raw material. If you want to be the best, you have to be the one who gets those last percentages, in yield, everything.”
Schwerin’s focus is on using AI and ML to create a recipe that vessel owners and crews can use to get the highest quality product from any given Carsoe system. “If we’re cooking shrimp and the temperature needs to go up, or we need to freeze them longer, we want the system to tell the operator. Or even do it automatically,” he says.
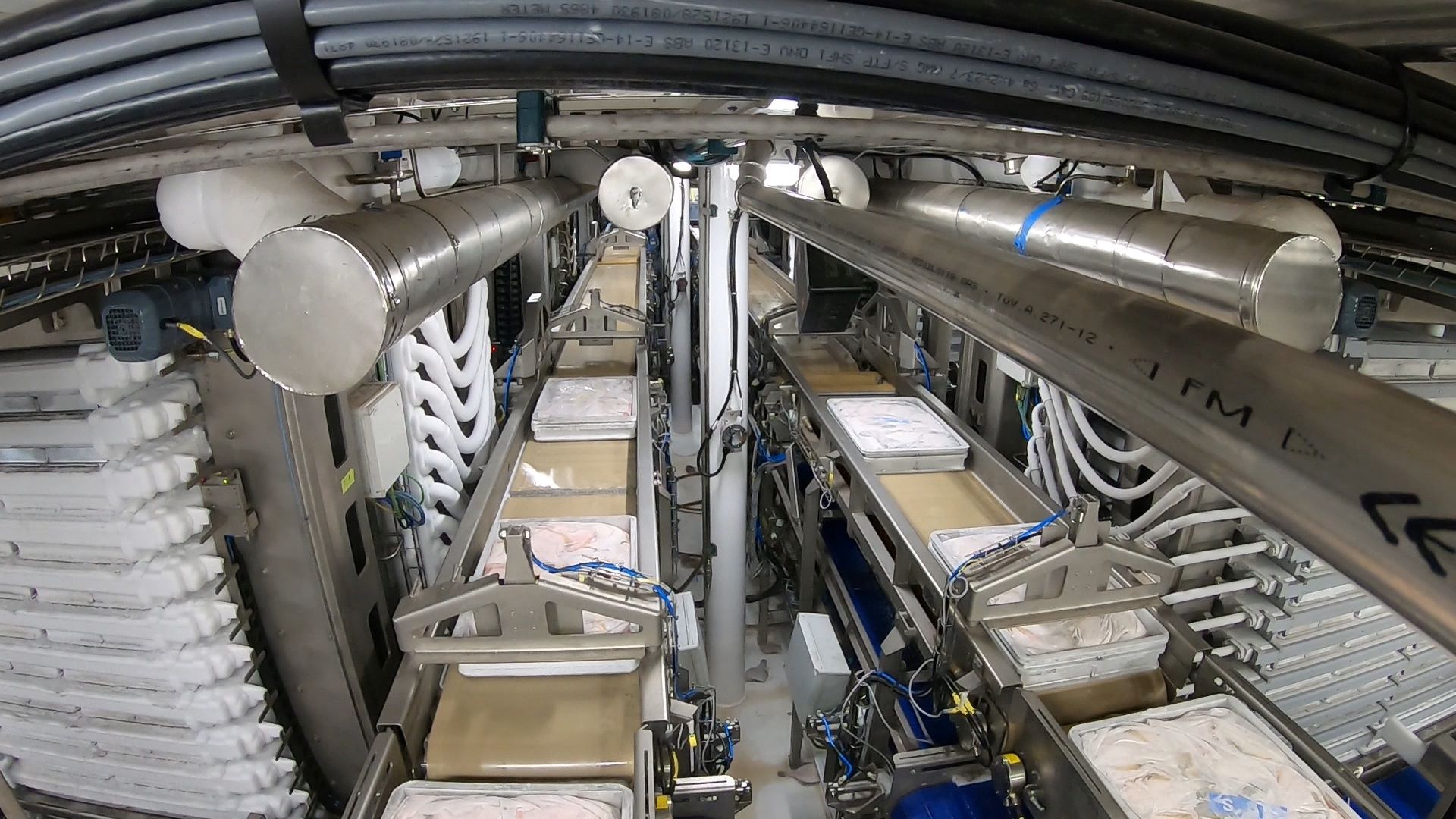
Machines can learn to do that, but they have to be taught, and to teach them, Schwerin and the Carsoe team require big data sets. “We’d like the fishermen using our equipment to share their data,” says Schwerin. “If they put their data into the pot, they will all get more information, and that will help us help them deliver a higher quality product. Everyone will get a higher price.”
Schwerin notes that the economic models Carsoe uses show a 3 to 5 percent price increase based on improved quality. “If you have a 5 million dollar trip and get another $250,000, then over a year, that becomes a substantial amount of money, with almost no investment. You don’t have to buy new equipment; change the way you use the equipment you have.” Schwerin notes that making the same amount of money on fewer fish will also bring down the cost of production by reducing wear and tear on machinery, cutting labor costs, and shortening time at sea.
Schwerin believes ML can take the data from many boats and determine what boats are landing the highest quality product and how they are doing it. “We can start to create a recipe for adjustments and identify which adjustments to make in real-time.”
If fishermen can make more money on the quality of the fish they’re landing rather than the quantity, they can fish smarter, Schwerin points out. “If fish are coming fast, but that is taking a toll on quality, AI can tell the skipper when it makes sense to set the net again. It might be better to wait and let the fish get through the system before catching more.”
To make this prospect a reality, Carsoe is collecting and storing data and working with computer experts at the University of Aalberg, among others. We are establishing a foundation for an AI setup so that we can act quickly when things become more developed, and the industry is ready for this,” says Schwerin. “We have a software program called Production Insights that collects data from the machinery and sensors throughout a system. This can also help you keep track of the status of your machinery to schedule maintenance and avoid breakdowns."
While the onboard processors prepare to join the AI bandwagon, Schwerin notes that the land-based processing industry has been using AI and ML for several years, although CNN is increasing the ways it can use it.
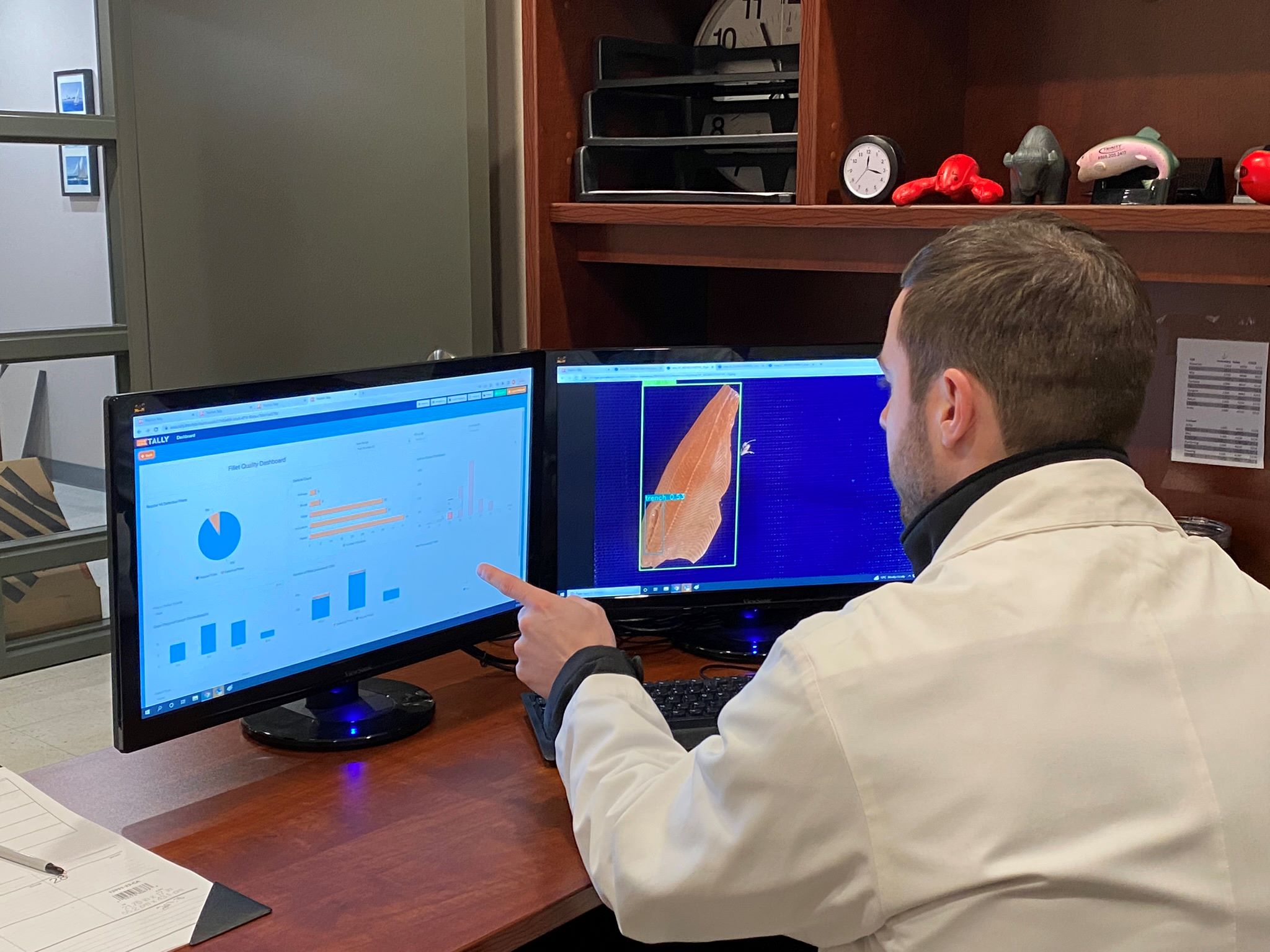
ThisFish Inc., based in Vancouver, is among the companies working to bring AI to the onshore processing industry. “Our role begins at the point where the vessels unload and create receipts,” says ThisFish CEO Eric Enno Tamm. “We have customers worldwide using our software to track their products through the supply chain. We also have customers in Alaska who are linking our software to the E-Landings and eliminating all that paperwork. Our software can track species like tuna that a company may own, but might be on a boat, in cold storage, or being transported. We can digitize that raw material and provide companies with fully visible electronic information on where their fish are.”
More than that, Tamm notes that the ThisFish software can be used to tell a story. “In the Gulf of Mexico, for example, the shrimp those guys are landing needs to be branded and differentiated from the huge volumes of farmed imports. I’d like to find some of those processors to work with. The Gulf shrimp story needs to be told, and traceability can help connect consumers to the story of their seafood.”
Tamm adds that the ThisFish software can be used to trace the path of seafood through the supply chain and help to identify IUU products by integrating with databases like Global Fishing Watch. “In the future, machine-learning AI could be used to spot outliers that might indicate illegal activity, like the way credit card companies do.”
ThisFish has been providing its traceability and digital workflow platform since the company began in 2018. In addition to improving those services, Tamm has ideas on how he’d like to use AI to improve the functioning of seafood processing systems. Like the team at Carsoe, Tamm’s objective is to improve quality.
“We work with customers like Orca Specialty Foods who process salmon from Bristol Bay, and they sometimes see lots of fish where half the fish have defects,” Tamm says. “There’s gaping and trenching in the fillets. They grade them now by taking a random sample of 20 fish and extrapolating. But we could potentially grade every fish in real-time with smart cameras and computer vision. In the future, we could have a paddle on the line that sorts defective fillets to a different line.”
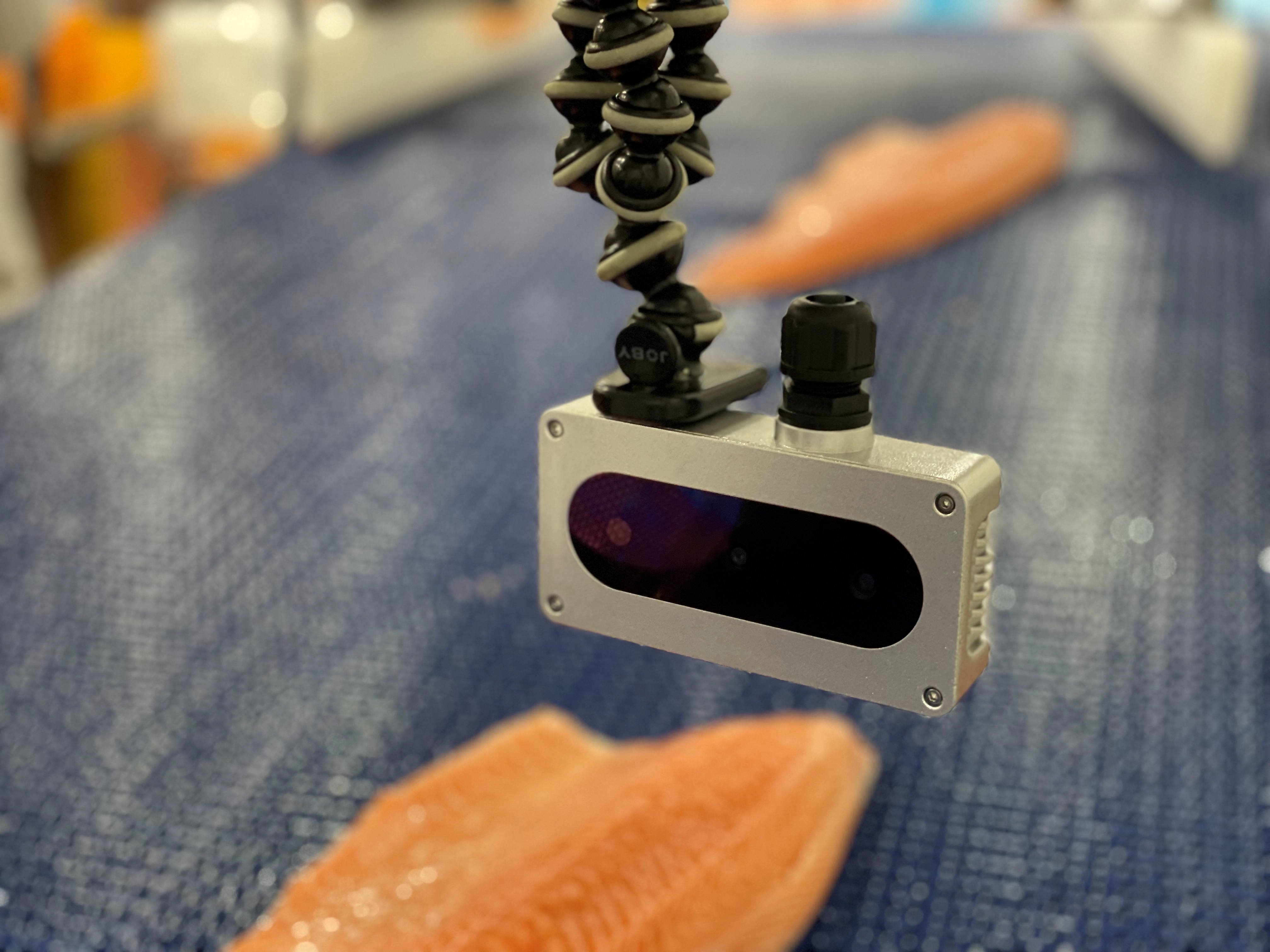
Tamm grew up salmon fishing on his father’s troller, and improving the quality of wild salmon and the price it commands in the market is important to him. Combining processing hardware and software with improved tracking programs, Tamm envisions tracing every salmon back to the boats that caught them. “If we can do that, we could base end-of-season bonuses on quality,” he says. One place that might be easy would be on the new processing barges operating in Alaska. ThisFish is working with Circle Seafoods on computer vision algorithms to automatically grade salmon by species, size, and other attributes.