Brooks Trap Mill, headquartered in Thomaston, Maine, is an integral part of the lobster industry. The dominant species of oak in Maine is red oak, often called piss oak. 'That’s it,' said Steve Brooks, co-owner of Brooks Trap Mill in Thomaston, Maine. 'I remember that smell, especially when it’s green wood, just cut.' Brooks Trap Mill has been a fixture on the coast of Maine since 1946, and Stephen, now 54, has been working there since he was a kid in the 1980s.
'I did everything when I was a kid,' said Brooks, who shares company ownership with his older siblings, Mark and Julie. 'When we were making wooden traps, I bent bows, drilled yokes, turned spindles.'
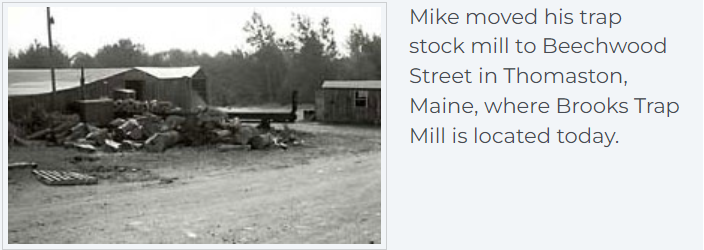
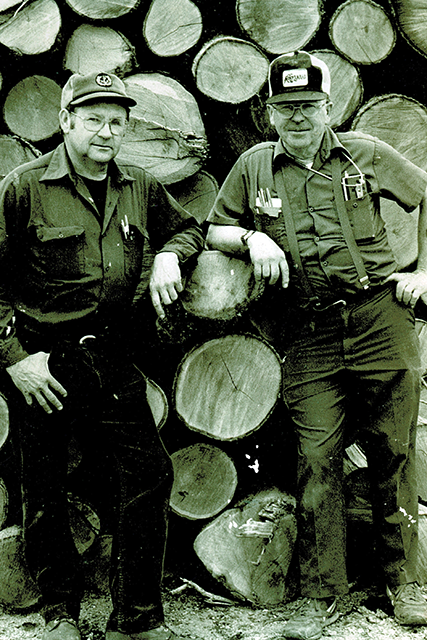
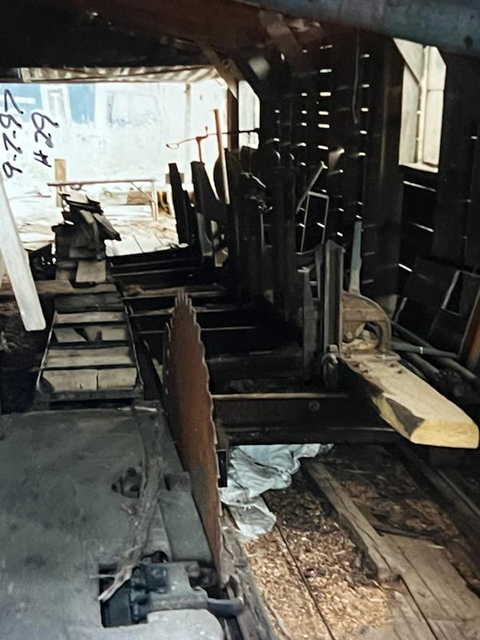
According to Brooks, the original mill—started by his grandfather, Mike, and then taken over by his father, Karl—cut more than trap stock. 'They cut the keels for a couple of boats built around here,' he said. 'Then in the 80s, as lobstering became more important, they focused exclusively on traps.'
Brooks’s father, Karl, temporarily left the mill to get an education. He earned a Ph.D. in psychology and taught for many years in Florida. 'He came back to the business in 1973,' said Brooks. A year later, Karl and his brother Lawrence built a much larger facility on Beechwood Street in Thomaston and officially named it Brooks Trap Mill.
'Wire traps started flourishing in the late 1980s,' said Brooks. 'But we still built wooden ones for the old-school guys. But by the end, the traps were just wooden frames with wire tops, bottoms, and sides.'
By the early 1990s, Brooks was building only wire traps. 'Originally, we had a machine to cut the wire where you had to crank it in by hand and align it, and then push a button, and a pneumatic shear would slowly cut it. But you always ended up with a row of prongs on one side, so cutting those off was a two-step process, too.'
In 1994, Karl Brooks invented a new cutting machine that made the process more efficient. 'He had it built with two blades, so it cut the prong off at the same time it cut the wire. And it is all computerized, so it’s self-aligning, and you punch in the number of meshes you want, say 16, and it cuts on 17, and the prong falls down into a container, and we recycle those.'
Besides recycling the prongs, Brooks noted pridefully that the company has gone green in a few ways. 'We have 382 solar panels on the roof that supply almost all our power for the year, and we can sell some back to the power grid,' Brooks noted that although his father also invented a machine to cut and bevel the red oak runners on the bottoms of the traps, they mostly use alternative runners, including some made of recycled plastic. 'The company that makes them takes big bales of plastic that used to go in the landfills and makes the runners and other products.' Brooks is open to change on the plastics issue and looking for ways to reduce plastic going into the ocean. 'We’re using all biodegradable plastic wrap when we wrap the pallets loaded with traps, and we’re looking at biodegradable bait bags. If people have ideas, we want to hear them.'
Listening has been a big part of Brooks Trap Mill's success. 'We get feedback at shows like the Maine Fishermen’s Forum and the Massachusetts Lobstermen's Assoc. Annual Weekend, and we talk with our customers,' shared Brooks. 'Somebody might ask for something, and then if we have more people ask for it, and we see that it could be good for the whole industry, we might incorporate it into the trap and make them all like that.'
Brooks noted that, presently, more fishermen are asking for 1-inch shrimp mesh for the heads of the trap—the entrances. 'We usually make them out of 2-inch stretched mesh,' he said. 'But some guys think the shrimp mesh fishes better and are willing to pay a little more.' On other occasions, fishermen have brought turn-key solutions to Brooks. 'We have what we call the Cappy Sargeant door. Cappy fished out of Milbridge, and they fish trawls. Sometimes, the rope would get caught under the corner of the door and peel it open. So, Cappy designed a door where the corners are bent down into the trap, and we offer that now.'
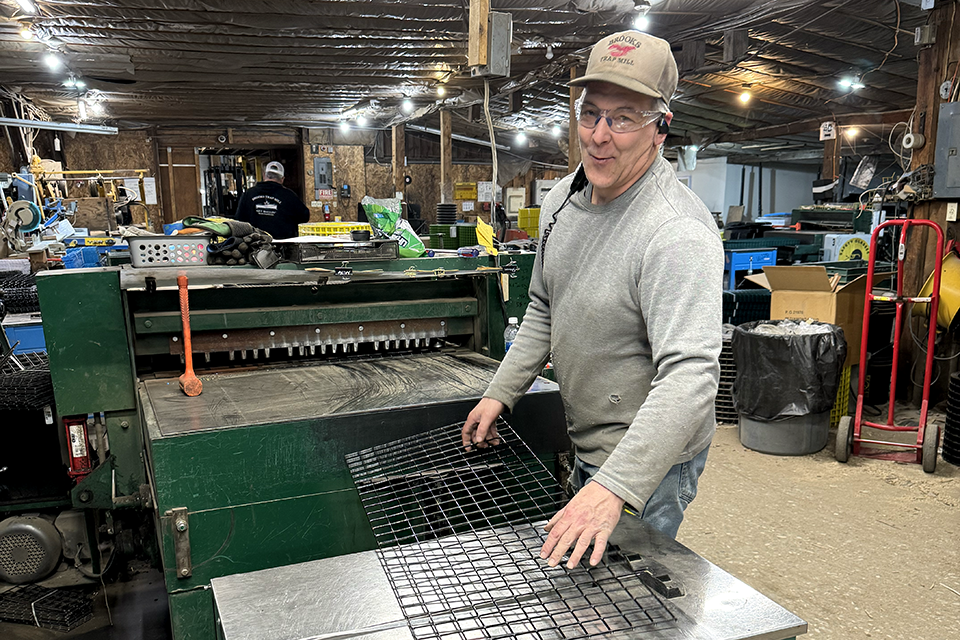
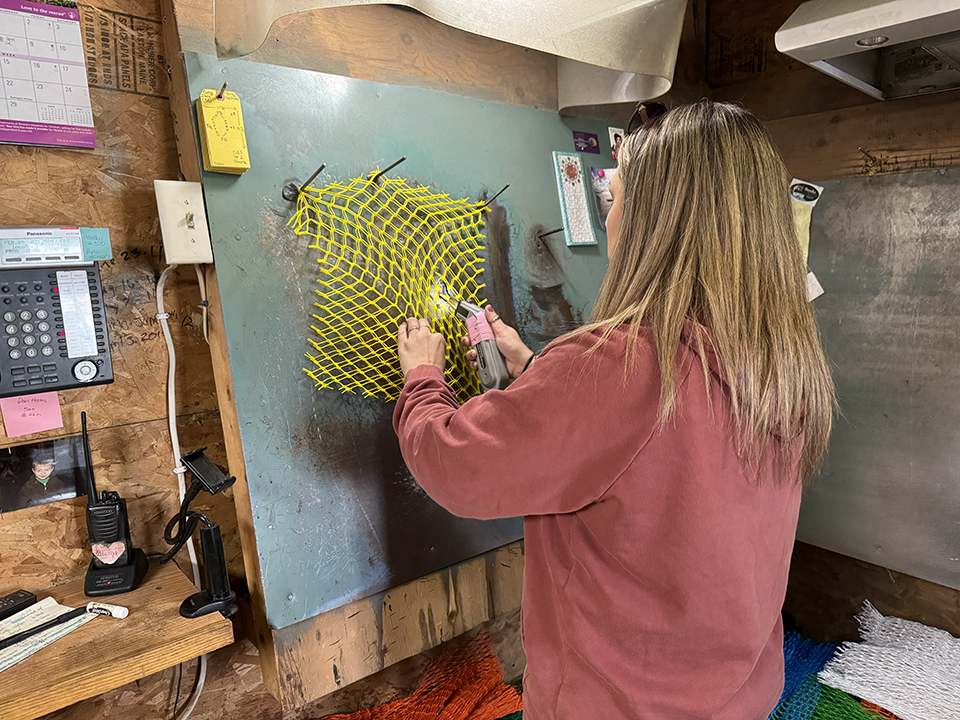
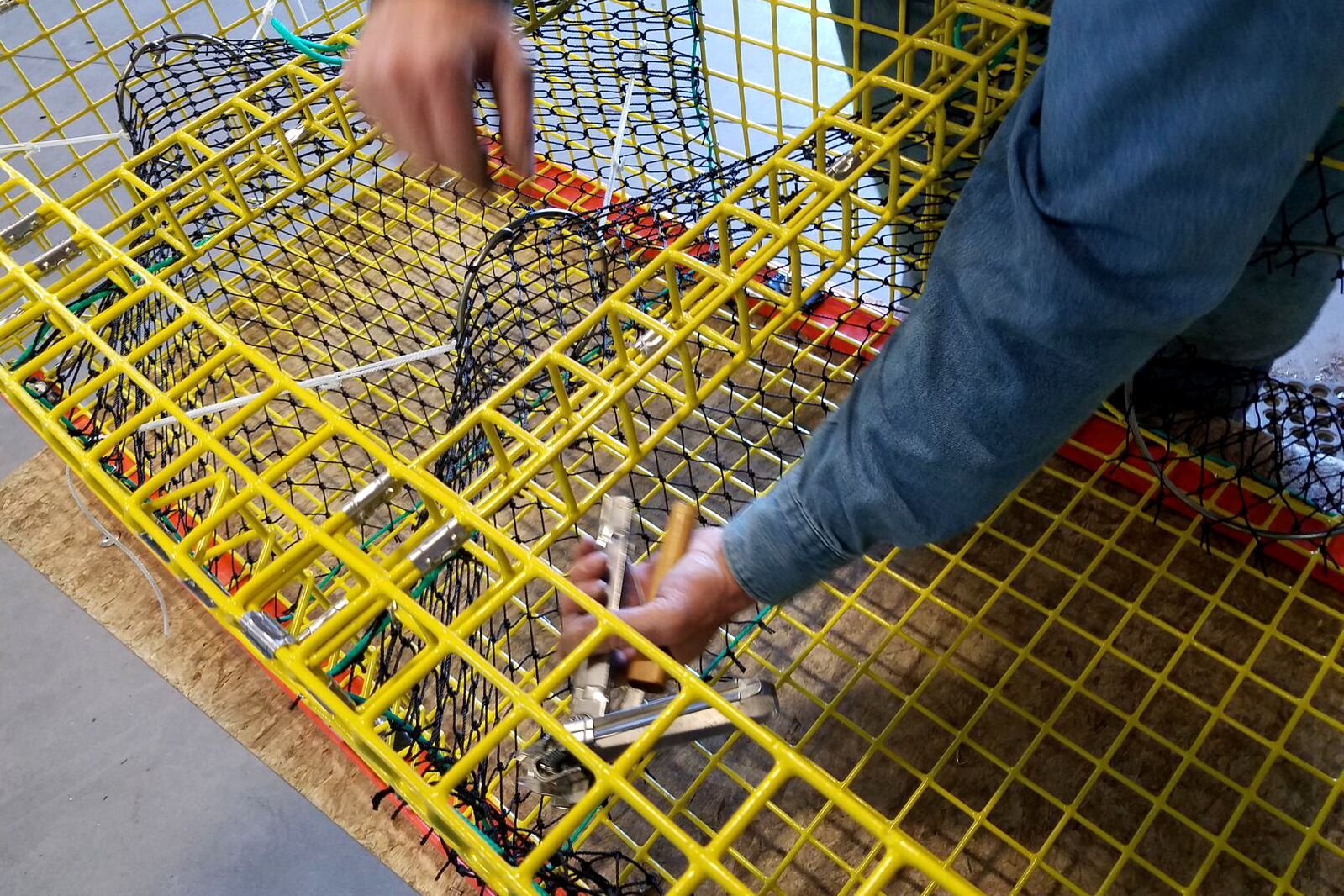
What makes the traps so customizable is that they are still hand-built. 'Once the box is shaped, you still have to clip them together, clip the ends on and the doors,' shared Brooks. 'They use a pneumatic clip gun, but there are still over a hundred clips to a trap and 100 hog rings for the heads, and we have to cut all the heads and weave the hoops in. It’s still a very labor-intensive process.'
Brooks Trap Mill has 120 employees and expanded beyond Thomaston over the years. In 1987, Brooks opened shops in Portland, Bath, and Jonesboro, Maine; in 2018, the company opened its newest location in Wakefield, Rhode Island. 'We don’t make traps in Rhode Island,' said Brooks. 'We sell our products and other supplies there.' Besides lobster traps, the company now makes all types of traps, including shrimp, eel, sea bass, and conch.
Brooks noted that one of the beautiful things about being a multigenerational company is forming relationships with multigenerational fishing families. 'Our customers who used to come in with their kids, now those kids are coming in, sometimes even the grandkids. We’ve become friends.'
At the Samoset Resort in Rockport, ME, you can catch some of the Brooks Trap Mill team up at the Maine Fishermen's Forum this Thursday, Feb. 28.