When Eugene Evans, 67, of Crisfield, Md., was growing up in the isolated fishing village of Rhodes Point on Smith Island, Md., his life dream was to become a commercial waterman.
As a youth, Eugene spent summers working with his father on the family boat, Twilight, harvesting peelers and soft-shell blue crabs and messing around with boats. At an early age, it was apparent, he could come up with ingenious ways of fixing anything related to boats.
Evans married his childhood sweetheart, Rose, in 1970. And at age 17, he went to working the water full time. With decline in the seafood industry, the couple moved off the island in 1973 to Crisfield on Maryland’s Eastern Shore. Evans continued to work the water, but more and more he was receiving calls from commercial fishermen wanting him to work on their boats. Over time, he was spending more time working on boats than fishing.
In 1980, the couple started Evans Boat Repair. He built his first fiberglass boat in 1983, a Smith Island crab scrape boat, known on Tangier Island as a barcat. The style of boat evolved over time specifically to pull a dredge by hand for blue crabs in the grassy shoal waters of Tangier Sound. The boat style goes back to days of sail and wind power.
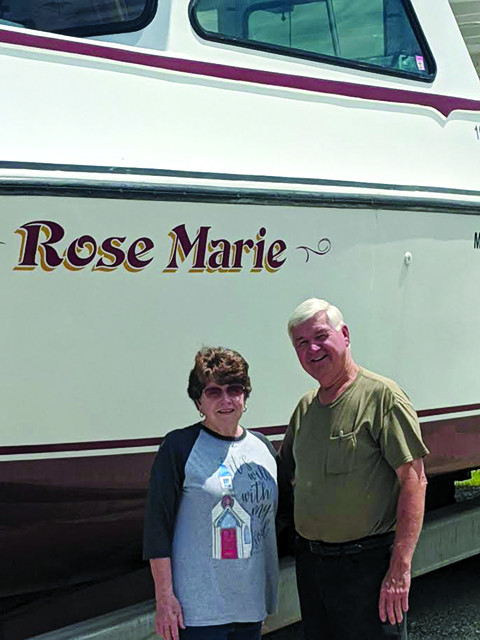
Evans’ father, John, owned a 22-foot barcat built during the sailing era. When Evans decided to use it as a mold to build a fiberglass version, it still had the slotted centerboard, which had been plugged when the first engine was installed. “I actually took her and turned her upside down and used her as a plug to build my first fiberglass boat,” he says. “She was an old boat, but she had features that worked good for working the waters of Tangier Sound.
“She was a slow-going boat because she had a sailing-style tuck stern. I squared the stern up on my (fiberglass) version and put a tunnel in her for the shaft and prop. The tunnel made her able to work in 12 inches of water on a soft bottom,” he says.
“When we got her done, I soon built and sold two more to a father and son. I had no intention of becoming a full-time boatbuilder. I ended up building five boats that first winter,” says Evans.
The next year, 1984, a waterman requested a 30-foot barcat. “I got (Smith Island boatbuilder) Joe Kite to build a 30-foot traditional wooden crab scrape boat, and I used it as a plug to build my fiberglass boat,” says Evans. Kite was paid by the hour to build the wooden boat and came daily to Crisfield from Smith Island to work on the boat in Evans’s boatshop. The 30-foot fiberglass barcat was a successful endeavor for Evans Boat Repair and he built and sold several more that year. Kite stayed around for the launching of the first fiberglass 30-foot barcat. He was later featured in the article “C-flex System sparks Maryland builders’ shift to fiberglass” in NF June 1989.
“When Joe saw our finished product, he called (the late) Dave Sintes (of Seemann Fiberglass) and had him design him a boat. After that time with me, Joe didn’t build many boats out of wood. It was all fiberglass,” says Evans.
In 1985, Evans began getting requests for larger, more traditional deadrise boats. He teamed up with a Trappe, Md., boatbuilder, the late Gene Travers, to design and produce the well-known fiberglass Somerset 35- and 42-foot boats. Over the years, the firm built deadrise fiberglass boats for commercial fishermen up to 50 feet long.
Evans says his business success has been “strongly tied” to his family, with Rose, his wife; Christina, his daughter; David, his son; and his grandson, David Jr., all working together in the business.
Working the water
Growing up in that Smith Island fishermen’s culture, Evans’ heart and soul was strongly tied to working the water. In 2017, he turned over the day-to-day operation of the boatshop to his son and grandson, and went back to working the water.
He is crab-scraping in the warm-weather months, and dredging and patent tonging for oysters in the winter.
“What is great about all this is that I’m doing what I want to do (work the water) and making two or three dollars in the process,” he says. “When I was a young man I loved working the water. Now that I’m old, it is just great to re-experience the feeling that you get when you have had a good day working the water.”
In 2017, he converted an Evans 30-foot pleasure boat, that he had built a decade or so before, into a commercial fishing boat. The main change was to install a new inboard engine. The boat had been powered by two outboard engines mounted to the stern. Evans installed an inboard 320-hp 3208 Caterpillar diesel engine.
While working the boat over the past three years, Evans found out its limitations. The draft on the 30-footer limited access to some shoal waters when scraping for crabs and house/pilothouse was not large enough to accommodate living conditions during the oyster season.
When dredging oysters on St. Mary’s River, on the western shore of Maryland’s Chesapeake Bay, Evans, who lives on the Eastern Shore, had to motor the boat across the bay and have someone bring his truck and camper across the Bay Bridge for overnight stays at a campground.
“This was not particularly comfortable, and it was expensive,” says Evans. “I needed a larger boat with less draft to accommodate my fishing needs.”
Rose Marie
Over the winter, when he was home from oystering, he built himself a new solid glass 40' x 12' x 28" fishing vessel. He named the boat Rose Marie, after his wife of 49 years.
“When Rose and I were first married I had (the late wooden boatbuilder) Maylon Green of Deltaville built my first boat, and I named it Rose Marie,” says Evans. “The first 50-footer we built here at the shop was on speculation and I named that boat Rose Marie. The man who ended up buying it changed the name.
“I figured this boat is going to be mine for a long time so I named it Rose Marie,” he says. “The first and last boat I’ve owned are named for Rose.”
The Rose Marie is, to say the least, non-traditional as Chesapeake Bay style boats goes. It took a creative mind and an experienced boatbuilder with time, means, shop and boat-lift availability and a willingness to experiment, a bit. That boatbuilder had to be Eugene Evans!
Several years ago, a firm in Oklahoma City, hired Evans Boat Repair to design and build a fiberglass flat-bottom “scow style” tour boat for a zoo to carry a maximum of 50 passenger on a lake.
“I designed it and built a mold for it, and we built a couple of boats for them,” says Evans. “When I started thinking about the Rose Marie, I knew I needed a larger hull size for more house space. I also needed a shallower draft boat for crabbing and a boat with a 12-foot beam.” An attractive part of using the scow design to Evans was the 12-foot beam because his boat slip cannot handle a wider boat. “I could have used one of my standard 38-foot deadrise hulls, but the beam is 13.5 feet, and I can’t get that in my boat slip,” he says. “I also thought I could improvise to make the scow style hull work for me.”
At the start of the project, Evans added a slight V into the flat-bottom. Historically, Chesapeake Bay commercial fishing boats require a deadrise V in the bow to cut through the bay’s choppy seas when underway. Evans also installed what he refers to as a “Deltaville hump.” On wooden deadrise boats, the rise in the stern is shaped by installing a reversed solid-piece horn-timber attached near the end of the keel. This extends the length of the boat and creates a concave bottom at the stern. This feature results in a smoother ride when the boat gets up on plane, and Evans says it creates less draft. The 40-foot Rose Marie draws 6 inches less water than the smaller 30-foot boat that he was working before.
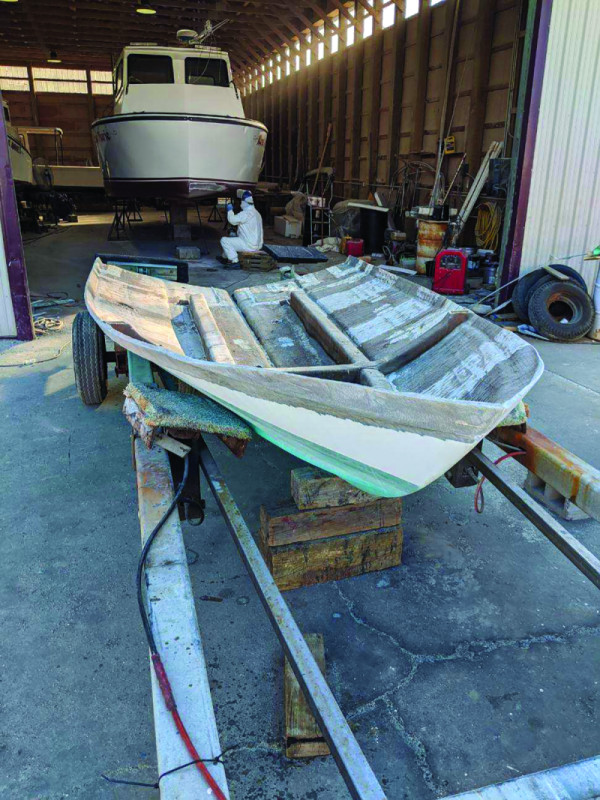
After completing the boat, however, test runs revealed there was considerable pounding coming from about 10 feet back of the bow, and the boat had a tendency to “blow-off” from a dock. “I knew right away I had to modify the bottom,” says Evans.
He looked about his yard and spotted an old Chris Craft hull about ready for the dump. He took that hull and cut 15 feet out of the V-bottom and glassed it to the bottom of the Rose Marie. He also added a skeg to the bottom that runs from the bow 12 feet aft to keep the boat steady in blowing winds and seas.
The new vessel is powered by a Cummins diesel engine rated at 210 hp working through a 2:1 502 Twin Disc reduction gear. During the first test run in May, before adding more V in the bottom, the boat reached a high speed of 22 mph. After the new V-bottom was installed, the boat lost 5 mph. This prompted Evans to rebuild a used 250-hp Cummins diesel, and he was planning to install the engine over the summer. “It’s not just speed I’m after,” he says. “I need a little extra power going through the water when I’m pulling my dredge and patent tongs.”
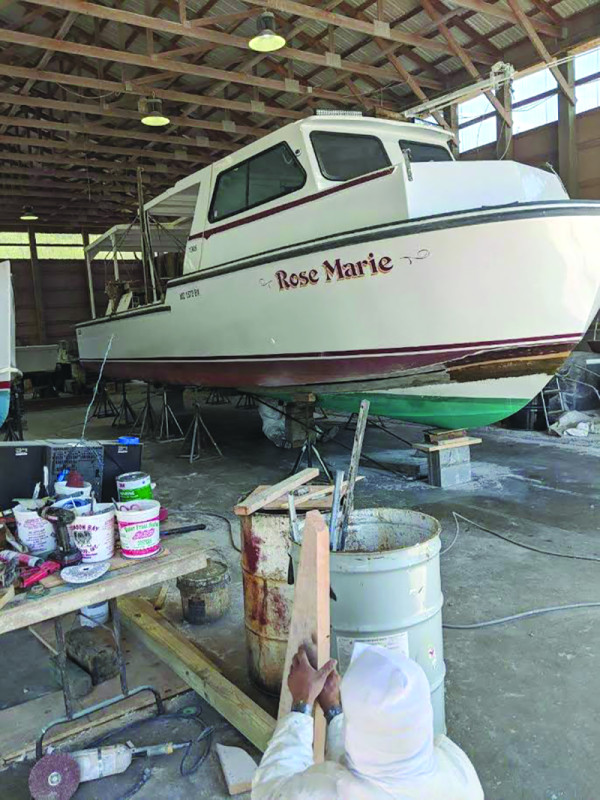
The new hull style enabled him to increase the height of the sides, which along with an enlarged trunk cabin, gave him more space down below.
“I’m 6' 2" so I need some height below (in the cabin),” says Evans. To create even more standing room height in the cabin, there is no ceiling (raised floor) where the V-berth, galley and head are located. “When I step down into the cabin from the pilothouse, I’m standing on the bottom of the boat. For comfort, I need all the height I can get.”
The house on the boat is filled with home comforts, as Evans has installed a head and shower, hot and cold running water in the galley and head, a twin mattress bed, and an oil furnace, along with a heater that works off the engine to keep him warm in the winter.
“When I go to St. Mary’s River to oyster next winter, I want to be comfortable,” says Evans.
The Rose Marie has a hardtop fiberglass canopy that protects him the from elements. It runs from the back of the pilothouse to transom. On the starboard side of the canopy, a 4.5-foot wide portion of the roof has been cut out. It tapers down to 3.5 feet and is 4 feet deep. This allows space for the dredge or patent tongs to swing onto the boat and room for the culling board.
The mast/boom is made out of stainless steel pipe and is hinged. So when it’s not in use, Evans can fold it down on top of the canopy. He installed an electric winder to lower the mast and boom down onto the canopy. Two other holes are cut in the canopy to access from the work deck the main winder, block, sleeve and line. Hatches cover those holes when equipment is not being used.
During cold-weather months, Evans will use clear side curtains that run the length on the port side and across the stern to keep weather off him. On the starboard side, curtains run up to the work space opening.
Always looking for a deal, Evans found used Wynn Enterprises front aluminum marine windows from a boatbuilder on the western shore. “I paid $200 apiece for them, and they normally cost $500 to $600 apiece,” he says.
“When I started this project, I knew there was going to be some trial and error involved,” says Evans. “I’m used to it. I’ve spent most of my life experimenting and looking for a better way to do things. A challenge is always exciting, and this boat has been a challenge.”
“The Rose Marie is going to work just fine for me,” says Evans. “She is going to take me out on the fishing grounds and bring me home safe, and I’m going to be much more comfortable working and living on the boat than I was before.”
INSIDE THE ROSE MARIE
Home port: Crisfield, Md.
Owner: Eugene Evans
Builder: Evans Boat Repair,
Crisfield, Md.
Hull material: Fiberglass
Year built: 2020
Fishery: Oysters and blue crabs
Length: 40 feet
Beam: 12 feet
Draft: 28 inches
Engine: 250-hp rebuilt Cummins diesel
Power train: Twin Disc 2:1 reduction gear, four-bladed, 22" x 21" Michigan prop, 1-1/2-inch stainless steel Aquamet 17 shaft
Fuel capacity: 149 gallons
Hold capacity: 18,000 pounds
Electronics: Furuno 1712 radar, Garmin GPS 50S, Lowrance SideScan Elite-9 and two VHF radios
Deck gear: Two Char-Lynn winch motors and two winches locally made by Kevin Marshall of Marshall Welding and Fabrication, Crisfield, Md., to hoist anchor and to operate hydraulically powered oyster dredge