Gordy Wright of Wright Built Boats in Irvington, Ala., is building a 22' x 7' glass-over-wood, flat-bottom Mobile Bay oyster skiff for Logan Kellum of Weems, Va.
Kellum, 17, is the son of Tommy Kellum of W.E. Kellum Seafood in Weems, one of the largest oyster packing firms in Virginia. The younger Kellum works on private state leased oyster grounds in Cockrell Creek and Great Wicomico River in areas too tight between the shores to drag an oyster dredge.
Kellum uses scissor-like hand “shaft” tongs to work the grounds and has been working out of a 17-foot Carolina Skiff that is not a very conducive platform for working hand tongs.
Mobile Bay and Chesapeake Bay oystermen work hand tongs standing on the washboards of their boats. Holding onto the shafts, they drop the tong heads to the bottom, grab a tong head full of oysters, pull it up to the surface, swing the tong heads over the gunwales, and drop oysters into the bottom of the boat — all in a smooth motion.
Washboards on the Carolina Skiff are too narrow for standing, which means Kellum has to work his tongs standing on the deck floor or on the narrow bow deck. This requires more arm strength to raise tongs up and over the side, and eliminates that smooth motion of ease.
The Kellums and Wrights know each other through their oyster businesses. Gordy’s brother, Stan Wright, owner of Wright Brand Oysters-Seafood in Bayou La Batre, Ala., heard about the issues with the Carolina Skiff and suggested switching to a Mobile Bay oyster skiff.
The skiff has blunted ends and will have a 3-foot-long fantail built off the stern and around where the outboard motor will be located. The fantail provides extra space for carrying payload and allows easy access to the motor “when getting a crab pot line out of the prop,” says Gordy.
Mobile Bay oysters are marketed in sacks that hold between 80 and 100 pounds of oysters. There is currently a six-sack day limit. “When they’ve sacked their oysters, they throw the sacks up on the fantail out of the way from where they are working,” says Gordy.
The Kellums also plan to use the skiff as a platform for planting seed oysters. The skiff can be converted to a seed barge. Wright is building an aluminum deck cover that will lay flat on the gunwales, spanning the open space from the house located near the stern forward to the bow deck. Seed oysters can be mounded atop the aluminum deck and planted either by shoveling or blowing overboard with a high-pressure water hose.
The bottom is made of 1/2-inch fir plywood with 3/4-inch plywood in the stern. The framing and other structural elements are made of salt-treated pine. Stainless steel nails are used as fastenings, and hull and decks will be fiberglassed. The boat is going to be powered by a 50-hp outboard. A covered helmsman station will be installed near the stern.
“The boat works great on Mobile Bay,” says Gordy. ”It is going to work good, too, in the creeks and waters, where Logan is working on Chesapeake Bay.”
Moving up to Virginia, Tony Ferguson of Gloucester County, Va., has his 1971 wooden deadrise up on the hard at Deltaville Boatyard in Deltaville, Va.
When boatbuilder Grover Lee Owens built Ferguson’s 34' x 10' deadrise in 1971, there were 21 active commercial wooden boatbuilders in Deltaville, and now all are gone or retired.
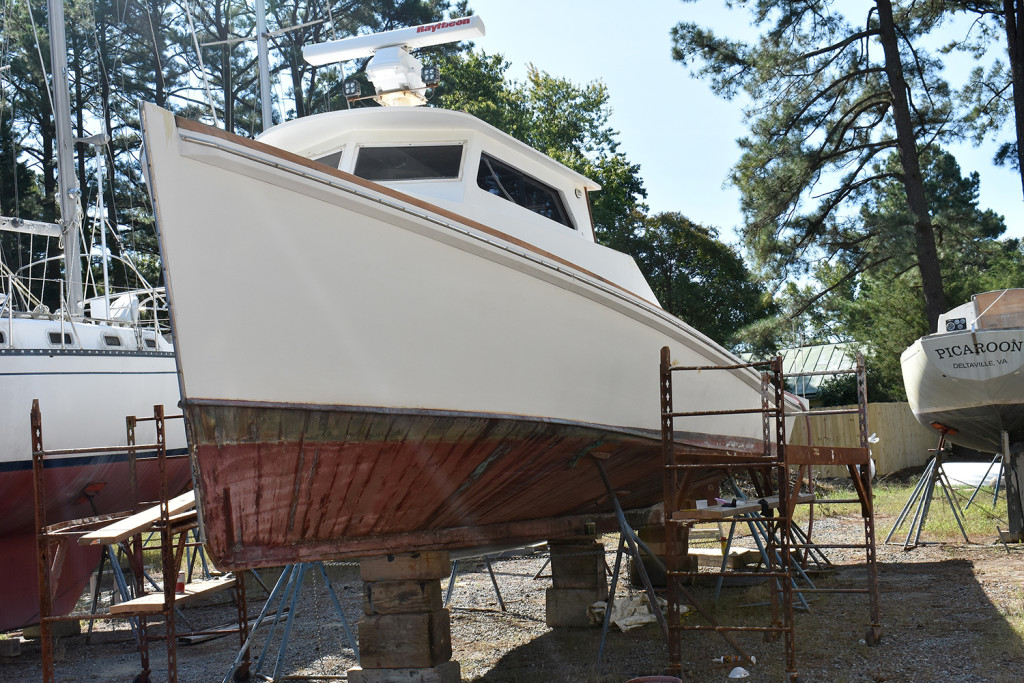
Deltaville’s location on Chesapeake Bay enhanced its wooden boatbuilding heritage that spanned from the late 1800s to early 21st century. Even though wooden boatbuilding has declined, the location of Deltaville on the bay and the infrastructure associated with a maritime community is still alive and thriving. Boats are still king in Deltaville!
Keith Ruse, owner of Deltaville Boatyard, has a growing business. The yard has a field where commercial fishermen and recreational boaters are allowed to work on their own boats. Ferguson has his boat up on the hard for routine maintenance.
Ferguson is an owner of the family owned retail seafood store Miss Mary Seafood in White Stone, Va., and works his boat to provide oysters and crabs for the store.
Deltaville Boatyard can do most anything when it comes to boats — from custom woodworking, fiberglass and steel hull repair, and engine installation and repair. Since January during this pandemic, Ruse has increased his workforce by 20 percent.
In the spring, Ruse is replacing a 75-ton boat lift with a 100-ton lift and is building a 25,000-square-foot climate-controlled service facility. This will open up 10 new job positions, he says.