Now that the Alaskan snows have melted and the waters have warmed, fishermen who did overwinter modifications or built new boats are about to launch their creations for the season ahead. They’re putting away the fiberglass rollers and acetone, shutting down the welders and paint guns, and getting ready to swap out the smells of molten metal and chemicals for the scent of saltwater.
Twin Tuition
Though many in the Bristol Bay gill net fishery know Mike Fourtner as the Cummins sales representative, he also sets his nets in the bay during June and July each year.
He’s been at it long enough that after last year’s season, it came time to replace the main engine on his own aluminum gillnetter, the Bonnie B.E.E.
Therein, he discovered an irony, he says. For eight years he’s helped others find solutions in their engine-swapping conundrums; now it was time to go through it himself.
“I’m glad that I had to go through the pain and agony,” he says. “There truly is really no better way to be effective at your job than to put yourself in your customers’ shoes, and for me to go through these last eight months, it just feels like it gives me a very unique perspective about how to be better at my job with Cummins.”
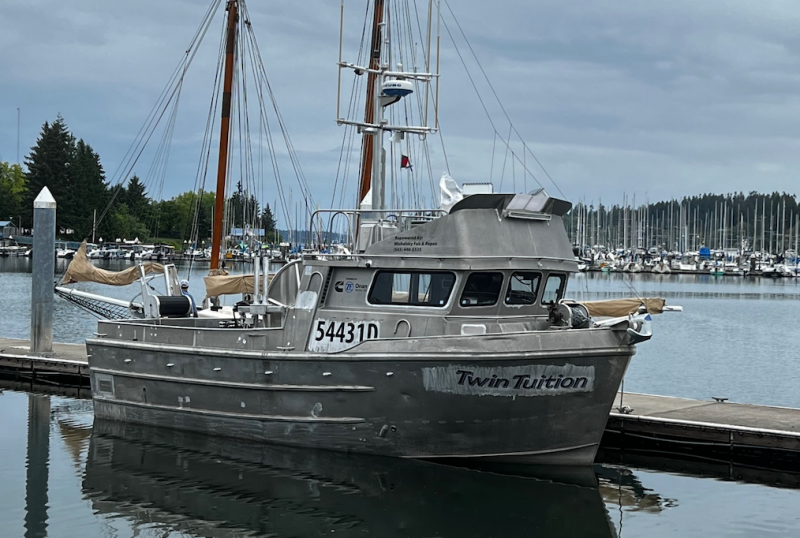
Fourtner, known for countless repowering solutions across Alaska and much of the West Coast, could have stopped with just an engine swap. Instead he amplified the experience by refurbishing other systems on his 1987 Jumbo Vito, built by Hydraulic Fishing Supply, in Anacortes.
“The wiring was taped together, and the hyrdaulics were all crazy. I went, ‘Man, I just want to gut this thing so bad.’ ” Last September that’s exactly what he did. Fourtner sent the boat south to his shop in Adna, Washington, and ripped it apart stem to stern.
By November the Bonnie B.E.E. had been reduced to a bare hull.
“It was two straight months with a plasma cutter. You should see the pile of scrap outside of my shop,” he says. “I wanted all new wiring, all new stainless hydraulic lines. I didn’t want to scrimp, didn’t want to cut any corners,” he says.
As for his power, the choice was clear: a Cummins.
“I pulled out a 6068 John Deere with 201 horsepower and went with a Cummins QSM 11, 670-horse Cummins. It’s triple the horsepower, so we upped the shaft diameter and put on a five-blade propeller.”
With the addition of new decking, a cabin, a new galley, new berths, new glass, custom-fit tanks and new deck gear, Fourtner basically built a new boat.
The boat was renamed the Twin Tuition, after his 8-year-old twins Ella and Emma, who helped on the project and want to head north to Bristol Bay with him this season.
“They’re good little helpers,” he says. “They want to come to Bristol Bay. They want to pick fish. So I named the boat the Twin Tuition, after the two, and they’ll be on the back deck, twins, learning how to pay for tuition.”
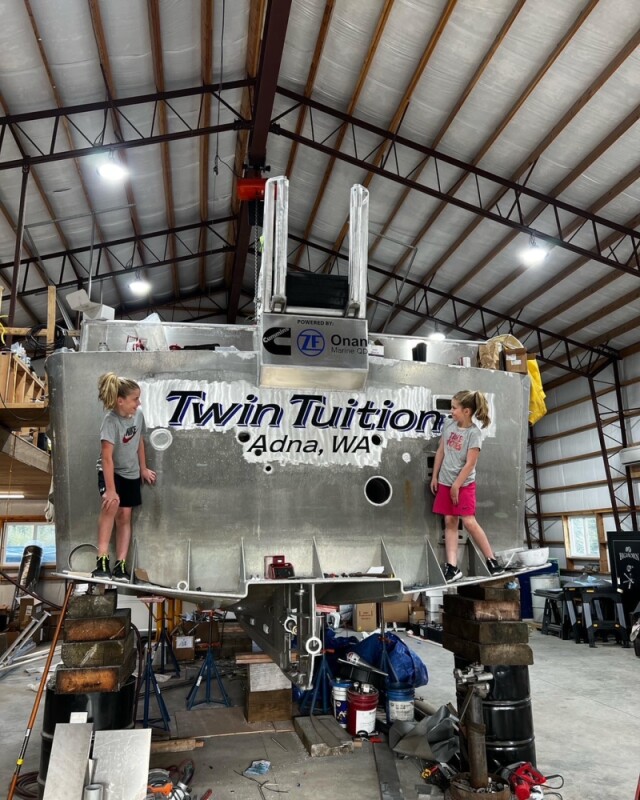
As for his own costs, Fourtner confides he could have never afforded the project if not for producing the work in his own shop. According to his calculations, he completed the work at about half the cost he would have incurred had he opted to build a new boat from scratch.
Like many of his customers, Fourtner experienced the overwhelming, clock-conscious worries of having the Twin Tuition ready as the calendar raced toward this year’s salmon season.
“There were no family vacations this winter,” he says. “Every day was a vacation day in my shop.”
On May 30 he readied the boat for a run to Vancouver, where he’ll load it as deck cargo aboard a large tender headed for Bristol Bay.
When he gets there, he’ll race around the various harvest districts at a top speed of around 18 knots. The original Jumbo Vito plowed through the water, bow heavy, and at a speed of just 6 knots, he says.
The refurbished Twin Tuition gained weight over the former Bonnie B.E.E., but the extra few thousand pounds of weight has been distributed aft, allowing the boat to get on step. That combined with the new 670-horse engine should give the boat a new level of performance, says Fourtner.
As for the upcoming season, Fourtner plans to spend extra time drumming up business for Cummins. If you’re running around at cruising rpms and putting out a grand plume of black smoke this summer, you might just meet him, business card in hand and willing to talk about a massive project ahead.
New Dawn
Brothers Reuben and Clifton Ivanoff had their vessel New Dawn prepped and ready early for what is expected to be an outstanding salmon season this summer.
“A lot of guys who complete their preseason work in July are getting done in time for June,” says Reuben, who along with brother Clifton have fished Alaska waters in their 52-foot Hansen since 2000.
Though they do most of their boat work in their homeport of Kodiak, the brothers drydocked the family-owned vessel in Seward in May for sandblasting, a fresh paint job and the installation of a new anchor winch and new picking boom.
Additional work included a new davit, a renovated fo’c’sle, new bunks and carpet, a new wheelhouse bunk, new ceiling material and new wheelhouse glass windows to replace the existing Lexan. The Ivanoffs are fans of Rain-ex, and look forward to a better view from up top when the windows are wet and they’re bucking toward the sun.
“I don’t know if the boat’s ever looked so good,” says Reuben, just days after they’d returned to Kodiak.
While the brothers repowered the boat with a new main engine in 2006, Ivanoff says repowering again is imminent among future improvements to the boat.
“The work on a steel boat never stops,” he says.
He added that others in the Kodiak fleet are completing ameliorations to their boats earlier than usual in anticipation of record harvests and rumors of record ex-vessel prices this season. The salmon season opened June 1.
Besides seining sockeye and pink salmon, the brothers and their crew work the New Dawn with pots for Pacific cod, tender for sea cucumber divers and fish for tanner crab when there is a season in local waters.
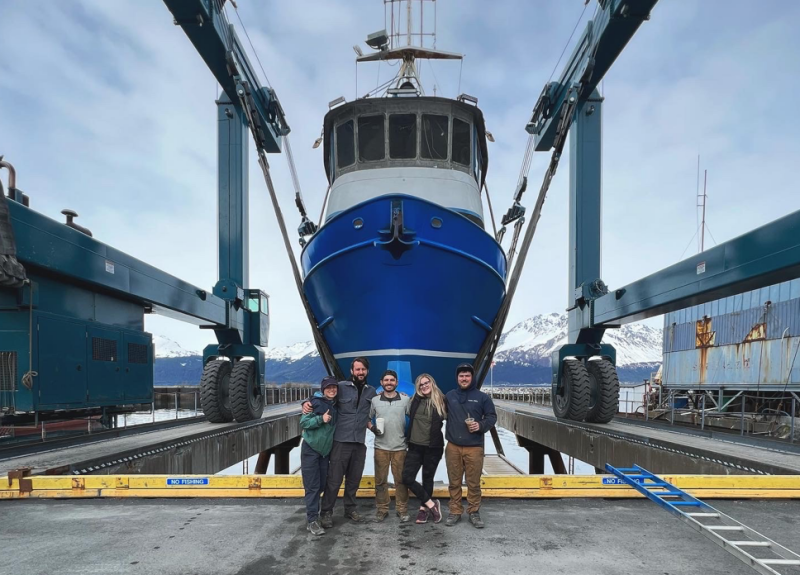
And…yet to be named
Randy and Kent Sandvik are no newcomers to innovation. National Fisherman featured them in 2018 for their work in conjunction with Lowell Stambaugh in the fabrication of compound rudders. As it turns out, rudders aren’t the only thing cooking at the Butte, Alaska shop.
Last December, Randy began building what will become the fourth gill netter to roll out of his shops. He’s built three in Alaska and one at a shop in Washington. Though he says that he’s borrowed ideas from other builders, he’s added plenty of personal touches to the offsets.
“It’s a one-off,” he says. “It has a different shape, and I wanted a little different boat.”
Thus far, the newest boat remains unnamed, but like other details, Sandvik says they’ll fall together in time. The 32’x16’ gillnetter is scheduled to fish Bristol Bay this summer, but Sandvik will make refinements to the boat in coming years. Among future additions, he has allowed space at the bulwarks, amidship on the port side, to fabricate a chute that will serve to pull his nets with the bow forward into the weather.
The boat will fish with mechanical controls this summer, although Sandvik plans to upgrade in the near future.
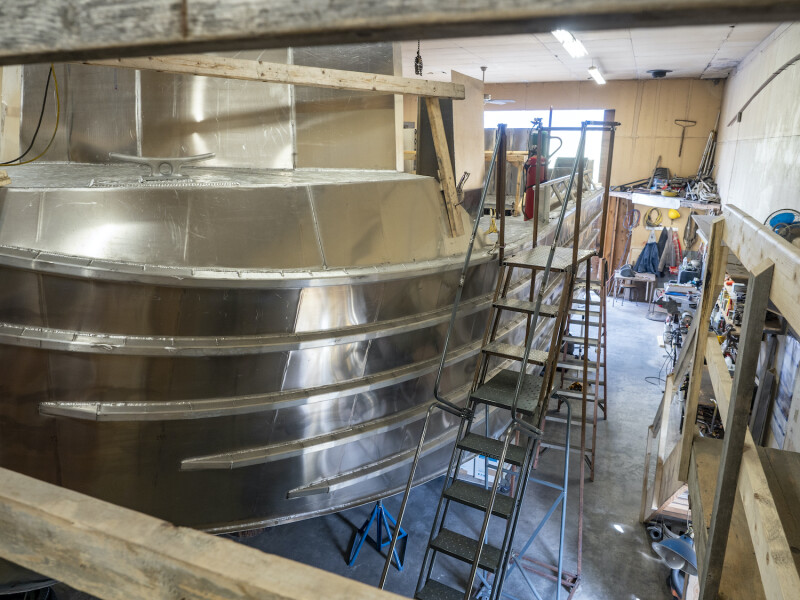
For power he chose two FTP inline engines, which put out 530 horsepower each, and coupled them to twin 17-inch Hi Jets, manufactured by Hill Innovations, Inc. Sandvik says he opted for the engine-jet combo with the hope of satisfactory mid-range performance. If his calculations work out, he says the combination will keep the rpms lower on the diesels but enable him to stay on step with moderate loads of fish.
“These jets work at medium pressure,” he says. “Fast jets make boats go very fast, but I’m actually looking for performance in the mid-range.”
Sandvik was asked about fuel economy with the jets.
“I don’t know what that will be,” he says, “But you make more than 500 horsepower in each engine, and it doesn’t matter what engine you’ve got, you’re going to burn fuel.”
On the back deck, the net will funnel through a power roller and onto a reel manufactured by Maritime Fabrication Inc. From there, the sockeye salmon will wind up in the hold, which can accommodate about 20,000 pounds.
The 10-ton refrigeration system is the very first of three units produced by Marine Refrigeration Solutions. Sandvik will run it hydraulically from his 35-gallon-per-minute system this year, but hopes to upgrade the unit to a diesel drive of around 30 horsepower to run the chiller and also provide about 6 kilowatts of electrical power.
“I’d like to have enough power to run a welder onboard,” he says.
Among other refinements to the new boat, Sandvik has incorporated an integral aluminum flip-up divider that stretches across the entire beam of the deck. The divider will separate fish from the lines, corks, leads and webbing when hauling the net over the power roller, picking fish, and stacking the net in the rear deck for resetting.
The concept of “overhauling,” as it’s known in Bristol Bay, is nothing new, says Sandvik, adding that the early fishery operated with net pulling deckhands, called “pullers” long before the advent of reels.
“Just because it’s an older way doesn’t mean it was a bad way,” he says of overhauling the net. He hopes that the pop-up checkerboard will save time in clearing a slugged net and getting it back into the water.