FPT Industrial, Motor-Services Hugo Stamp and Tom Aliotti team up with wrap artist Troy Dorn to make the Killer one of a kind
With trade shows shut down all over the world, diesel engine manufacturers need a new way to promote their products in a competitive industry. Justin Roeser of Motor-Services Hugo Stamp has come up with a novel way to sell FPT Industrial’s N67 570 EVO engine — a 6.7-liter, inline six that packs 530-hp into a tight footprint.
“I was creative director on the project,” says Roeser. “We were sitting around kind of brainstorming — how do we reach out to people and make an impact? We also had a budget we had to spend. FPT Industrial put the question out there, and my idea was: Why don’t we wrap one of these Bristol Bay boats?”
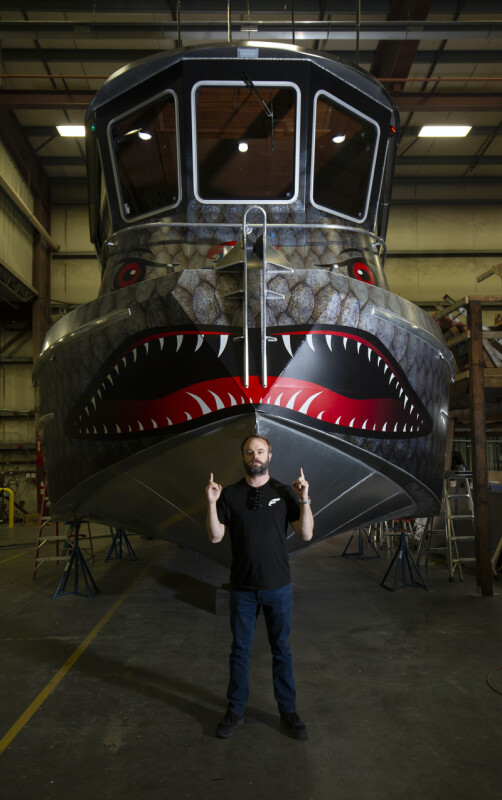
Roeser’s idea didn’t just materialize in a vacuum. He had heard of a Snohomish-based artist, Troy Dorn, who wrapped cars. Roeser proposed the idea to Dorn, FPT, and Tom Aliotti, builder of Bristol Bay gillnetters.
“My idea was to wrap a Bristol Bay boat with a killer salmon wrap,” Roeser said. “The word ‘killer’ is inspired by the ’70s heavy metal band Alice Cooper and their album by that name.”
Roeser’s idea was to take a sharp-toothed mouth, the kind used on World War II fighter planes, and combine it with the rainbow quality of a salmon skin. “I hooked up with Troy’s company, it’s called Gorilla Mad. They did wraps on cars. I’d seen their work on Instagram. They were able to take the ideas in my head and produce the artwork on a heavy duty 3M vinyl wrap.”
Working with Gorilla Mad, the team began tackling the challenges of putting a durable wrap on a hard working boat.
“We had to figure out how it was going to go on all the corners and rub rails and things like that,” says Roeser. “There is a film that goes over the wrap that lets it change colors with the light. It’s almost like a hologram. And all of the red — the mouth and the eyes — and the white teeth, all glow in the dark.” Roeser notes that the workers in Aliotti’s boatshop would come in early in the morning and feel the boat was staring at them.
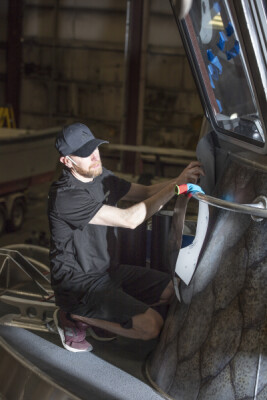
Before the wrap, came the boat itself. Roeser is selling engines, not wraps. Tom Aliotti’s fabrication company, NTG Fabrication, builds what Aliotti says is the best Bristol Bay gillnetter in the fishery (see NF August 2020, “A man on the inside”). With Bristol Bay boats limited to 32 feet in length, they have gotten wider and moved toward twin-engine configurations, like the 530-hp FPT that gets the boats up on step and hitting speeds of 40 knots.
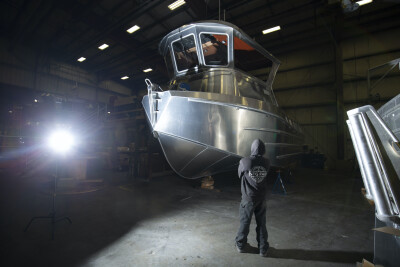
“The hull is basically the same that we’ve been building,” says Aliotti. “Our boat is pretty much refined; we don’t have to do too much. We’ve hit the Holy Grail in terms of performance and comfort.” The performance comes from Aliotti’s hull design and the power train. The FPT Industrial N67s are fitted with ZF 305 reduction gears at 1.275:1, which drive the pair of Ultrajet 340HT jets. The jet’s stainless steel, mixed-flow and aluminum, axial-flow design has proven itself over many hours, and it is supported by manufacturer Marine Jet’s aftermarket service.
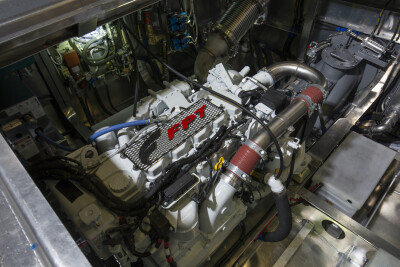
With the two other boats he built alongside the Killer, Aliotti has somewhere around 20 of these FPT Industrial engines in service. But with every boat there are always tweaks.
“We changed some details with the hydraulics and RSW and the way the fish hold is zoned,” says Aliotti. The boat has a 10-ton, hydraulic powered RSW (refrigerated seawater) system from Pacific West. Aliotti has zoned the hold to allow the skipper, Derrick Burns, to float different amounts of fish.
“If they have 7 tons, they don’t have to fill the entire hold.”
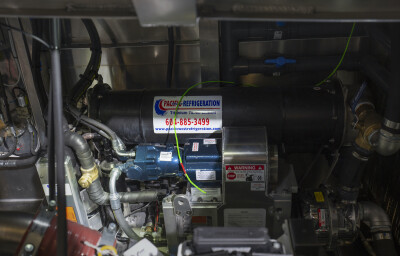
Aliotti is also very focused on problem-free hydraulics.
“One of the things that sets our boats apart is the hydraulic system that Seattle Marine and Steve Brooks put together,” he says, noting the quality of the material from Seattle Marine and caliber of Brooks’ work. “We run the system off both engines. One runs the RSW, and one runs the deck gear. But we can also combine them, and either one can run either system if we need to.”
For deck gear, Aliotti builds his own drums. “We build them in-house, so that we can take care of the details of how the net goes in and out with our stern roller.” Aliotti got the stern roller and anchor winch from Kinematics Marine Equipment. “But we make a custom slide stern roller that has this ram rod system that allows us to use it like a level wind.”
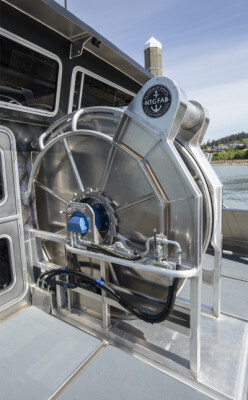
For electronics, Aliotti has installed mostly Garmin electronics.
“We have two plotters, two fathometers, power steering,” he says. “We have a camera system that is in the engine room, the deck, and the stern of the boat. We have two Icom VHFs.”
The fo’c’sle accommodates three crew members and the captain. “It’s tight but comfortable,” says Aliotti. “The captain’s bed is almost queen size, there’s big, 4x7 bunks for the crew.”
The galley has a three-burner stove with oven, and the crew can watch movies on a 33-inch TV. The shower is outside on the back deck.
“It’s good for you,” Aliotti says. “But yes, it has hot water.”
The boat took about five months to build, and it hit the water in early May 2021. The wrapping was the last big step.
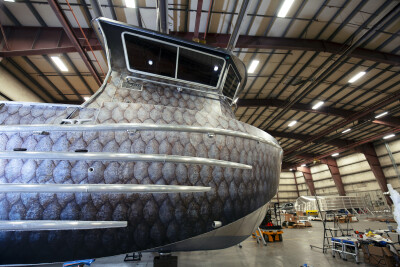
“We did it all in the shop,” says Aliotti. “I worked with Justin on that. It came out better than I expected.”
“The wrapping went quick,” says Justin Roeser. “But the project took a long time. There were a lot of visits to Tom’s shop. They did a rendering, took photos of it, came back with the artwork. It was months of preparation, little pieces here and there, and then the install with Gorilla Mad.”
Troy Dorn and another installer did the initial wrap in three long days.
“In my line of work, 12-hour days are not unusual,” says Dorn, noting that the biggest challenge of the job was the planning and preparation.
“I started talking to Justin back in December,” says Dorn. “The most important thing is that they were able to provide us with the CAD files. A lot of the boat is flat, but it’s important to know the shape. The cabin part, for example, on the corners — those pieces are totally rounded, so getting the artwork so that you know it’s going to match up and flow, you need to know that shape.”

Dorn worked on several iterations of the artwork, until Roeser and the rest of the team agreed on a final design. He ordered four 75- by 5-foot rolls of 3M vinyl.
“The standard film you would use is white, but because of the scale pattern we were doing, I ordered a specialty film that is very expensive and very hard to get right now because of covid,” Dorn said. “The base color is called light aluminum. It’s actually a silver metallic. And once we print on that, it gives the fish scales a very realistic look.” Once the material is printed, Dorn coats in with a laminate that protects against damage and UV radiation.
“Then we had to cut it and plan the install,” says Dorn. “There’s a lot of brain work that goes into making sure it all flows.” Once Tom Aliotti had the boat finished, Dorn and his helper came in. “It was a lot of work,” he says. “Prepping the boat and fitting around all the corners and on the sides, making sure all the FPT Industrial and Motor-Services Hugo Stamp logos lined up. Around the nose we had to stretch the film because it was higher than the 60-inch width of the roll. And it was a good thing they had a lift there. Sometimes we were 25 feet up, sometimes we were upside down. But it all worked.”
Dorn credits the good results to his meticulous planning. The good news is that Roeser wants to wrap two more Aliotti boats, and Dorn will have much of the prep work already done.
“We plan on doing more,” says Roeser. “FPT Industrial can be known for doing art boats. It’s a fun way to use a piece of machinery to make a visual impact and create a character people can talk about.”